

Some of the terms encountered, and their specific definitions are: Terms such as "hardness," "impact resistance," "toughness," and "strength" can carry many different connotations, making it sometimes difficult to discern the specific meaning. In metallurgy, one may encounter many terms that have very specific meanings within the field, but may seem rather vague when viewed from outside. I shall employ the word tempering in the same sense as softening." Terminology In 1889, Sir William Chandler Roberts-Austen wrote, "There is still so much confusion between the words "temper," "tempering," and "hardening," in the writings of even eminent authorities, that it is well to keep these old definitions carefully in mind.
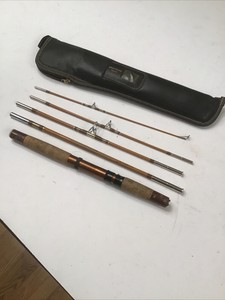
Tempering was often confused with quenching and, often, the term was used to describe both techniques. Many different methods and cooling baths for quenching have been attempted during ancient times, from quenching in urine, blood, or metals like mercury or lead, but the process of tempering has remained relatively unchanged over the ages. The process was used throughout the ancient world, from Asia to Europe and Africa. The oldest known example of tempered martensite is a pick axe which was found in Galilee, dating from around 1200 to 1100 BC. Tempering is an ancient heat-treating technique. Steel is usually tempered evenly, called "through tempering," producing a nearly uniform hardness, but it is sometimes heated unevenly, referred to as "differential tempering," producing a variation in hardness. Tempering is also performed on normalized steels and cast irons, to increase ductility, machinability, and impact strength. In carbon steels, tempering alters the size and distribution of carbides in the martensite, forming a microstructure called "tempered martensite". Many steels with high concentrations of these alloying elements behave like precipitation hardening alloys, which produces the opposite effects under the conditions found in quenching and tempering, and are referred to as maraging steels. However, in some low alloy steels, containing other elements like chromium and molybdenum, tempering at low temperatures may produce an increase in hardness, while at higher temperatures the hardness will decrease. Higher tempering temperatures tend to produce a greater reduction in the hardness, sacrificing some yield strength and tensile strength for an increase in elasticity and plasticity. Low tempering temperatures may only relieve the internal stresses, decreasing brittleness while maintaining a majority of the hardness. Precise control of time and temperature during the tempering process is crucial to achieve the desired balance of physical properties. Heating above this temperature is avoided, so as not to destroy the very-hard, quenched microstructure, called martensite. This is also called the lower transformation temperature or lower arrest (A 1) temperature the temperature at which the crystalline phases of the alloy, called ferrite and cementite, begin combining to form a single-phase solid solution referred to as austenite. Tempering is accomplished by controlled heating of the quenched work-piece to a temperature below its "lower critical temperature". Tempering is usually performed after quenching, which is rapid cooling of the metal to put it in its hardest state. The reduction in hardness is usually accompanied by an increase in ductility, thereby decreasing the brittleness of the metal. Tempering is a heat treatment technique applied to ferrous alloys, such as steel or cast iron, to achieve greater toughness by decreasing the hardness of the alloy.

Tempering reduces the hardness in the martensite by transforming it into various forms of tempered martensite. Photomicrograph of martensite, a very hard microstructure formed when steel is quenched.
